A recent trip to Leicestershire enabled me the opportunity to visit Leicester City’s training ground and catch up with Chris Minton, their newly appointed dedicated head mechanic - a new role created at the club by their visionary head groundsman, John Ledwidge.
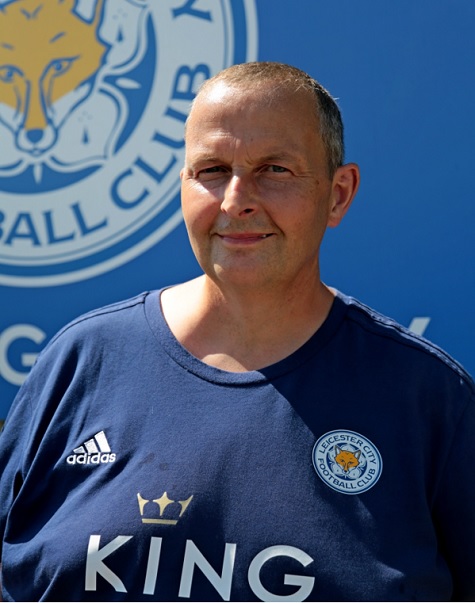
Chris Minton
Most of the Premiership football clubs now have larger training facilities encompassing many different types of pitches to manage plus a very busy fixture and training schedule to meet.
Gone are the days when you had a couple of mowers to mow the pitches. These new training facilities now require a larger fleet of machinery and resources to maintain them.
Currently the club train at their existing Belvoir Drive Training Ground that was purchased in 1963. Belvoir Drive has played a significant role in the Club’s development, which has gradually been extended by introducing a number of additional pitches and ancillary facilities.
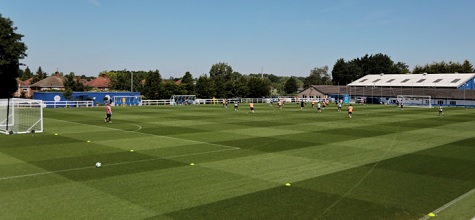
John manages a team of 14 staff and is actively involved in the ongoing development and investment in world class sports turf surfaces for the club whilst managing 24 acres incorporating 9 natural and re-enforced football pitches and 14 staff at the club’s training facility.
Having served the club well for many years, the Belvoir Training Ground is unfortunately no longer sufficient to meet the demands of a modern Premier League club. It is too small and constrained at all sides by neighbouring properties, which prevents the club from continuing to develop the facilities required for its ongoing growth and to support further success.
With all this in mind the club have been searching for a suitable site to develop that offers plenty of scope to develop their aspirations and compete with other Premiership teams.
Recent press coverage has said that the club have acquired Park Hill Golf Club and are seeking planning permissions to develop the site with the aim of building a brand new training complex on the 180-acre site.
The development proposals seek to retain and enhance the site’s valuable ecological features while at the same time providing: -
- Approximately 14 pitches, plus a mix of small pitches, goalkeeper and training areas.
- Full-size indoor pitch.
- Show pitch with a small spectator area for approximately 499 people.
- Foundation/full-time Academy and First Team building, including accommodation, training and educational facilities.
- Car parking facilities.
- Sport Turf Academy building.
- Ground maintenance building.
- Retain a nine-hole golf course for private use.
- Landscape and habitat mitigation and enhancements.
- Sensitively designed and sited secure boundary and screening.
Once completed it will certainly enable Leicester to compete with the best clubs in the league and offer their players some of the best facilities in the country. I am sure the attraction of the golf course facility will also attract a lot of interest and enable John’s grounds team to grow and develop many new greenkeeping skills.
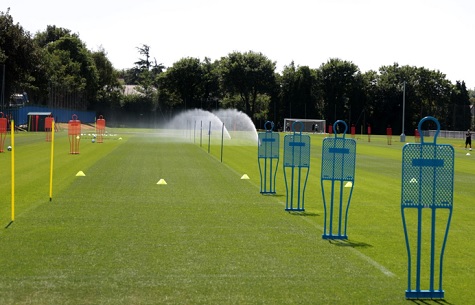
The demand for producing better quality playing surfaces and in particular improving club-training facilities has been born out of the needs of a modern-day footballer to be fitter, stronger, agile and faster while at the same time ensuring they remain injury free. This has led the need to replicate the stadium pitch-playing surface at their training grounds, providing consistent safe surfaces for all of the club’s teams from youth, academy and senior sides.
Therefore, in recent years we have seen a dramatic shift in the investment in machinery and resources at football clubs. These facilities are used on a daily basis, which in turn means that the grounds team are constantly preparing and repairing these playing surfaces.
During the growing season these playing surfaces are mowed and cleaned up each day, resulting in the need for a large fleet of mowers and machinery to cope with the demand of these pitches. The Leicester’s appointment of Chris as their full-time mechanic is a wise move by John who knows the full potential of having their own dedicated mechanic and workshops.
As for machinery the club currently have 4 brand new ATT infinicut’s, 6 Dennis G860s (34inch) mowers with cassettes, 21 Honda Rotaries, three Toro 3100 sidewinder ride-on mowers, a couple of Toro HDXD workmen fitted with sprayers, three Toro Procore 648 aerators a couple of Iseki tractors and other complimentary machinery / equipment such as Pellenc battery powered strimmers, blowers and hedge trimmers. They also have several line marking machines - all in all a lot of machinery to be maintained.
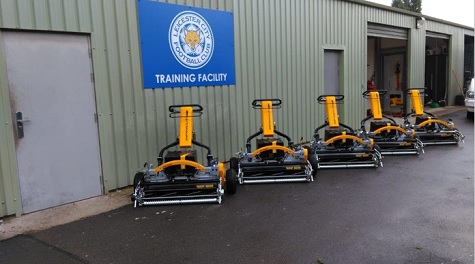
Chris’s new role is to manage and maintain this equipment and ensure the staff are trained to operate it safely. Chris brings with a wealth of experience having headed up the machine operations at the Belfry Golf club for 11 years.
However, to utilise Chris’s skills and expertise, the club have had to invest in providing a fully operational workshop with a range specific tools and equipment to enable Chris to do his job efficiently. Chris started is new role in September 2017 and one of his first jobs was to rearrange the garage and storage areas while at the same time bringing in some designated machinery aids such as a Sealey pneumatic hydraulic work bench, Draper tyre machine, air compressor (air tools) a set of 4000 DXI Bernhard Grinders a mig-welder, hot torch system and a press for removing bearings and a large two post hydraulic lifting ramp and finally a whole range of BETA hand tools and spanners.
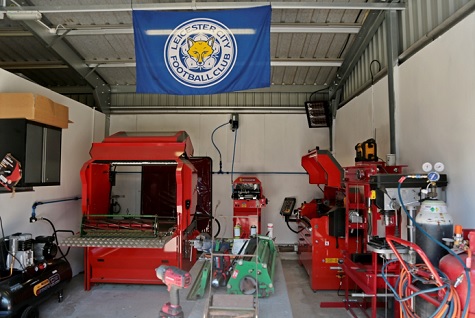
However, one of the real beneficial changes has been in the education and training of the staff with regard to respecting their machinery and being more accountable. Chris has put in place a full recorded preventative service schedule for every piece of machinery and equipment. Daily pre start check sheets are completed before any machine leaves the yard, Chris has also implemented a series of operational training days and pre start check training sessions ensuring all staff carry out appropriate pre-start and operation checks on the machinery they use and above all communicate daily with him on any specific issues and problems they may have with the equipment they are using.
Chris gets a daily list from Callum (Head Groundsman) of machinery that is going to be used the following day then Chris sets up the cutting units and checks over the machines.
Although based at the training ground Chris goes up to king power stadium at least once a week to check over the machinery that’s used there.
Chris uses his grinders regularly and grinds little and often keeping his mowers in tip top condition.
Chris likes to run his mowers on a light contact between bottom blade and cylinder, thus ensuring they are always cutting sharp and set at the correct height of cut (HOC) usually set between 23-27mm for the pitches at the training ground. This year the training pitches where renovated on the 14th May, with hundreds of tonnes of sand being applied. The sand does have a detrimental effect on the mowers, requiring them to be reground more frequently during the initial first few weeks of the summer. Servicing of the mowers is done in house, based on the number of hours used. A complete service of oil, and filters is also carried out.
The club buy their machinery from a number of local dealers, namely Marsdens, Platts Harris and Dennis Mowers.
It would seem from my visit that Chris’s appointment has gone down very well, with all of the grounds team led by Callum Allsop praising the work being done to make their job more efficient and effective. There is no doubt in my mind that the club’s investment in both Chris and the new workshop space has made a significant improvement in the management and maintenance of the pitches at Leicester City FC.
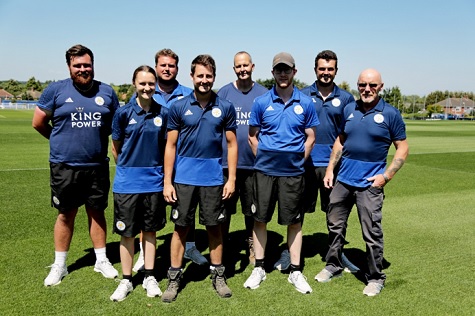
Coupling the club’s vision of the future with this exciting new training ground, it’s clear John Ledwidge and his team will be taking groundsmanship to new heights of expectation.