With lockdown still curtailing the opportunity for myself to get out and about in recent weeks, I have refocussed my time looking at the current state of our industry in terms of the maintenance costs of our natural turf facilities.
If you Google this information you tend to get a plethora of answers, which I find quite disturbing as many are extremely far from the reality of the true costs incurred maintaining a sports facility.
This is often made difficult by the sheer number of variables and the lack of understanding of what is required when managing and maintaining a given playing surface.
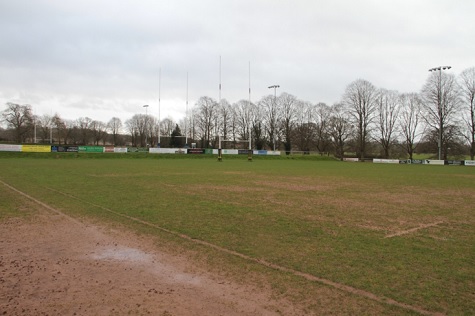
These variables are usually associated with the level of sport being played, the desired level of provision and the detailed level of inputs and maintenance operations that need to take place.
We must also take into consideration its expected level of usage, current condition, and problems it may well have in terms of surface drainage porosity and sward composition.
These costs will also be dictated by the way the work may be carried out, whether it is done in-house, by volunteers, by contractors or by paid employees?
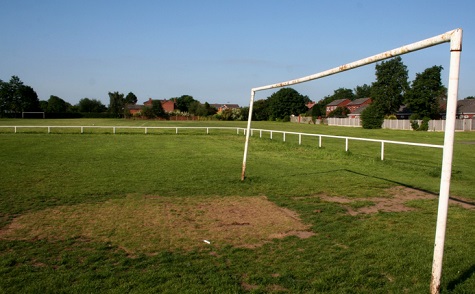
In most cases the level of budget being put aside for general maintenance of grassroots-level playing facilities tend to be way off the mark. One of the reasons for this is often the lack of understanding of groundsmanship and what is required in terms of inputs and resources that are necessary for the maintenance of their facility. No two sites are the same. Each have their own unique set of requirements and maintenance needs and inputs to either maintain its status or additional work to bring it up to standard.
Far too often, many clubs tend to do the bare minimum which can result in a basic set of maintenance inputs generally seen as, mowing, feeding, marking out and some minor repairs when warranted. Quite often they also skimp on end of season renovations, which over time leads to a deteriorating playing surface.
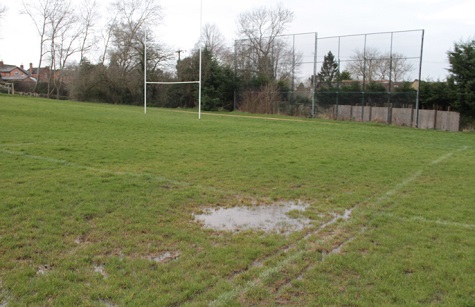
I firmly believe if clubs actually recognised the true costs and inputs required to maintain their pitch and produced a business plan to set to facilitate a way of securing the budgets to run the club, we would then start to see an improvement in club facilities and an increased level of sport participation.
Over the years I have written numerous articles on the subject along with contributing a regular monthly sports facility diary update. A recent article considered the need to get clubs to find the funds to invest in their pitches.
My Viewpoint article today is based on the fact we need to promote and be more aware of the potential costs required to maintain a range of sports facilities.
Having spoken to a number of groundsmen, it was felt the best way to estimate the annual maintenance costs for each sport was to put together a maintenance calendar for each and attribute the inputs undertaken and record the time taken for each basic maintenance operation - for example, grass cutting, feeding, aeration, weed control, fungicide treatments pre and post-match operations and renovations.
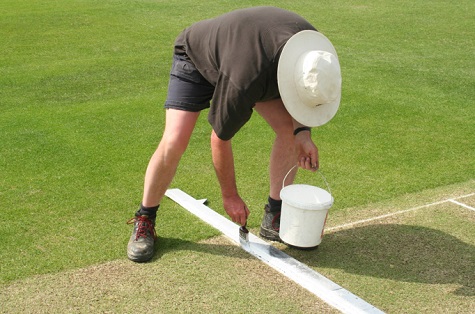
Overall, it was not surprising to see how much time is required to maintain a facility.
So for each sport, these are my findings based on a grassroots level of provision based on one single pitch facility :-
Football / Rugby
I based both rugby and football costs on a similar maintenance regime - essentially a weekly cutting programme during the growing season, using a compact tractor and roller mower, feeding programme, aeration work, marking out, strimming, pre and post-match activities, harrowing and a decent end of season renovation that includes overseeding, topdressing with 100 tonne of sand and an application of fertiliser.
In total the man hours for one person attributed to carrying out this work throughout a calendar year, equated to around 362 hours of manual work. A full end of season renovation cost would be in the region of £6000 and allowing a further £2000 for the cost of materials and servicing.
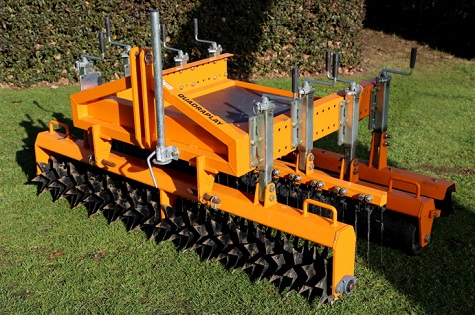
These figures are without the initial cost of the machinery you require for undertaking this work yourselves. In total the investment in tractors, mowers, and other essential equipment, line markers, outfield spikers etc, may cost the club in excess of £30,000 to buy.
Capital costs and replacement costs will need to be accounted for somewhere in the budgetary figures so that you are able to maintain and keep your machinery running. Today there are many types of finance deals available to secure machinery and equipment.
So, if you are in a position of being able to use volunteers your annual costs would still be in the region, considering the costs of materials / machinery servicing costs, of around £8000.
If you then look at the man hours, we equated to be 362 hours allocated to undertaking the work required to maintain your pitch, hourly charges for specific works can vary between £20-£50 per hour - therefore if we were to set a commercial rate of £30 per hour labour rate against these figures ( £30 x 362 hours), we would be now looking at a set value of work of around £10860 .
Therefore, employing someone or using a contractor to undertake the work with the cost of materials. The total annual cost for maintaining a grass roots rugby / football pitch would be near to £18860.
There will be some flexibility in these figures if you were able to scale up the amount of pitches you maintain, but in essence we should be looking at a future investment of around £20,000 per pitch.
Bowls
As for bowls, undertaking the same formular, working out the hours invested in time to maintain a bowling green, cutting three times a week and undertaking other relevant work, feeding, scarifying, verticutting and end of season renovations we came to a figure of 258 hours with end of season renovations, material and servicing costs being £3500.
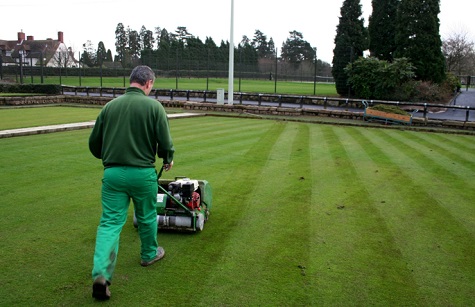
Therefore again, if you were to have a volunteer workforce and needed to cover the costs for machinery and materials you could be looking at a total annual cost of £3500 per green.
However, if you must pay for the services of a paid greenkeeper / contractor to undertake the maintenance work at a low rate of £30 per hour, then the total annual labour maintenance cost would be 258 x £30 = £7740.
Therefore total annual cost including labour and materials would be around £11420. Allowing for some unforeseen works etc we are probably looking at a baseline figure of an investment of £12,000 per green - similar figure seen on this bowls website.
Cricket
As for cricket, we come up with some surprising figures. We broke the work down into five key working areas - work completed on the square, outfield, auxiliary works, ten-day wicket prep and renovations during a typical calendar year.
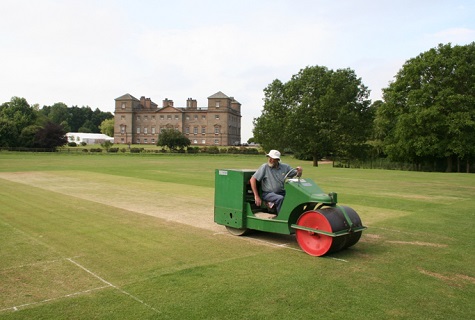
The following hours were attributed to each section:
- Square - this included pre-season rolling activities and maintaining square during the season 700 hours.
- Outfield - work associated with the outfield, mowing spiking feed etc 210 hours
- Auxiliary works - Moving covers, site screens, cutting hedges and other works 105 hours
- Ten-day preparation of wickets – preparing and repairing wickets 100 hours
- End of season Renovations – cut, scarify, aerate, seed and topdress with loam. 40 hours
Total hours incurred: 1155
Cost of materials: £3000
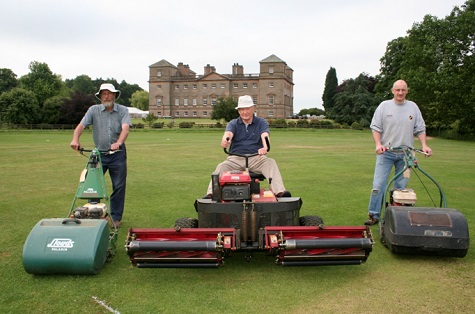
As for machinery, the clubs would need to be looking at an overall investment of £30,000 in machinery and equipment to undertake this work.
So, for a club with a strong volunteer group, the club would still need to allocate £3000 a year to pay for materials and machinery upkeep.
Again, using the same labour rate of £30 per hour to employ a groundsman / contractor to undertake the work we are looking at a cost of 1155 hours at £30 per hour = £34650
So, in reality we are looking at an investment of around £38,000 a year to maintain a twelve pitch premier standard cricket facility.
Realistic investments
These costs are an indication of the real investment of maintaining natural turf sport facilities. There will be possible savings and efficiencies when scaled up if you have more than one facility. But this investigation has shown when considering the skills training and regulations and work practices involved in maintaining a given sport facility, they come at a cost. And clubs should be more aware of these costs and plan accordingly and find the relevant levels of cash to maintain these excellent community sport facilities.
In my example I used a hourly rate of £30, a realistic rate in my opinion, for the services of a professional contractor / groundsperson who has all the relevant overheads, experience, insurances, machinery investment and taxes to pay on his earnings. Even if you reduce this hourly rate down to £20 per hour it still equates to the following annual maintenance costs for the above sports :-
- Football / rugby 362 hours =£7240 +£8000 = £15240
- Bowls 258 hours =£5160 +£3500 = £8660
- Cricket 1155 hours = £23100 +£3000 = £26100
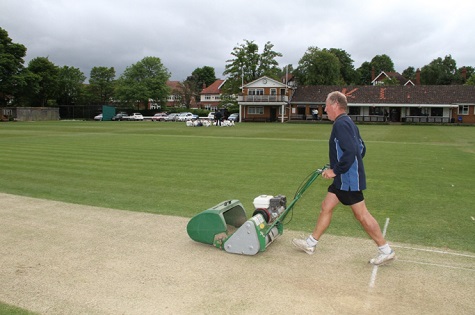
Clubs need to be charging a more realistic membership fee to help cover these costs associated with the maintenance of the facility. Given the cricket club’s annual figure of £38,000, if the club has 250 members that would equate to each member having to pay £152 per year to cover the maintenance costs.
For far too many years, sports clubs have not been charging members enough money to cover the cost of maintaining their facilities - bearing in mind if you or I were to join a fitness centre, we would be expected to pay £500 plus a year and still pay for drinks and food etc.
It is now time we started realising the true costs of providing good sporting facilities and begin investing for the future of these irreplaceable venues. I can see a massive uptake in sport and recreational pastimes once we get past this pandemic.
In my opinion you cannot put a value on the provision of sport in terms of the benefits gained over time for the members and local community who use these facilities. Let us hope, by June under the government’s roadmap to recovery, we will all be back playing and participating in sport.