A SIGN OF THINGS TO COME
Another step towards Brexit
by Service Dealer Ireland Editor, Alan Mahon
As of from yesterday (September 1st) the Irish government has implemented a new EU requirement change for the importation of certain plant produce and used machinery into the Community under Annex V of Council Directive 2000/29/EC.
As of from yesterday (September 1st) the Irish government has implemented a new EU requirement change for the importation of certain plant produce and used machinery into the Community under Annex V of Council Directive 2000/29/EC.
What does all this mean? Basically, it is another step towards preparing for Brexit. Before September the 1st this rule applied to countries outside the EU. The requirement is there to protect countries within the EU against the introduction, from countries outside of the EU (third countries), into the Community of organisms harmful to plant or plant products and against their spread within the Community. When the UK leaves the EU on October the 31st next, Great Britain will be classified as a third country.
According to a Trader Notice issued by the Department of Agriculture, Food and the Marine (DAFM), the new regulations for used machinery, which have been operated for agricultural or forestry purposes, require that, prior to export, the equipment is cleaned to remove any soil or plant debris. It must then be subject to an official inspection by the exporting country’s National Plant Protection Organisation (NPPO) to certify, by issuance of a phytosanitary certificate, that it complies with EU import requirements.
Specifically for Irish businesses, these new regulations will apply to the UK once it leaves the EU, regardless of whether there is a deal or not. There would have to be a specific, separate treaty established between the EU and the UK for these rules not to apply to the UK post-Brexit.
You can find out more information about this new regulation by contacting plantandpests@agriculture.gov.ie or by phoning 01 5058885.
With regard to new machinery sales into Ireland from the UK the rules of trade may not be as clear-cut after October the 31st.
Talks are ongoing between the Irish and UK governments about creating an ‘All Ireland’ trade deal for agricultural produce sold between Northern Ireland and the Irish Republic. Will this deal also apply to machinery used in agriculture and, just as importantly, machinery used in horticulture? Only time will tell. Many dealers in Northern Ireland are quite concerned on what the future holds when they sell farm and garden equipment into the Republic. Likewise dealers in the Republic also have concerns.
I hope common sense will prevail between the two governments and that a hard border will be avoided between Northern and Southern Ireland. Having borders re introduced would be a terrible outcome. One thing is sure though, you can expect more rules and regulations to follow.
Staying on matters economical, many machinery and equipment manufacturers have released their 2nd quarter trading results and most have shown a decrease in profits and/or income, compared to the same period last year. Is this the sign of an oncoming recession? We will have to wait for third quarter results (from September onwards) to say for certain. Now, more than ever, is the time to hang on to your existing customers and keep working hard to gain new ones.
 |
|
 |  |
BRIGGS & STRATTON POST "DISAPPOINTING" Q4 & FULL YEAR RESULTS
Q4 5.9% down, full year 2.4% down
The fourth quarter of 2019 capped a difficult year of "unprecedented market challenges and higher than expected operational inefficiencies" says CEO.
Briggs & Stratton Corporation in the U.S has announced financial results for its fiscal fourth quarter and year ended June 30, 2019 - describing them as "disappointing".
The company released the following analysis -
For the fiscal 2019 fourth quarter:
- Fiscal fourth quarter net sales were $472 million, a decrease of $30 million or 5.9% from $502 million for the prior year. Fiscal 2018's fourth quarter included approximately $20 million of accelerated sales in anticipation of the go-live of the company's upgraded ERP system at the beginning of fiscal 2019. Adjusting for this, net sales this year decreased approximately 2%. Shipments for the fiscal 2019 fourth quarter fell short of expectations primarily due to difficult market conditions caused by an unusually wet spring in North America compounded by near-term market disruptions caused by channel partner transitions.
- Quarterly GAAP gross profit margin of 14.4% and adjusted gross profit margin of 15.0% decreased from gross profit margin of 21.7% and adjusted gross profit margin of 22.1% last year due to sales mix, lower production volumes and operational inefficiencies. Challenges in labour availability restricted the Company's ability to more quickly remediate start-up inefficiencies related to the business optimisation initiatives.
- Fourth quarter GAAP net loss of $18.5 million, or $0.45 per share, included business optimisation charges, acquisition integration charges and a pension settlement charge. Excluding these items, adjusted net loss was $14.9 million, or $0.36 per share, as compared to adjusted net income of $0.47 per diluted share for the fourth quarter of fiscal 2018. The fourth quarter of fiscal 2019 also included a non-cash tax related charge of $5.1 million, or $0.12 per share.
For the fiscal 2019 full year:
- Fiscal 2019 net sales were $1.84 billion, down $44.7 million or 2.4% from $1.88 billion for fiscal 2018 primarily due to unusually dry weather conditions in Australia and Europe, lower storm generator sales and lower service parts sales, and near-term disruption caused by channel partner transitions, including the bankruptcy of a major North American retailer. Sales of commercial engines and products increased approximately 13% for the fiscal year.
- Full-year GAAP gross profit margin of 16.4% was down from 21.2% for fiscal 2018. Adjusted gross profit margin of 17.0% was down from 21.5% last year due to sales mix, lower production volumes and startup inefficiencies from the Company's business optimisation initiatives.
- Full-year GAAP net loss of $54.1 million, or $1.31 per share, included business optimisation charges, bad debt expense for a major retailer that filed for bankruptcy protection, a litigation settlement charge, a pension settlement charge, senior note repurchase premiums, a tax charge associated with tax reform and integration charges. Excluding these items, adjusted net loss was $12.9 million, or $0.32 per share.
Todd J. Teske, Chairman, President and Chief Executive Officer said, "We are clearly disappointed with the fiscal 2019 results. The fourth quarter capped a difficult year of unprecedented market challenges and higher than expected operational inefficiencies encountered during the ramp-up of our business optimisation initiatives.
"The North America lawn and garden market slowed considerably as the quarter progressed from unusually wet, cool spring weather compounded by near-term market disruptions with channel partners. Europe set record high temperatures in June and July to impede channel inventory reductions. While we achieved operational improvements on many of the business optimisation program start-up issues, continued inefficiencies offset the benefit of those improvements, including near-term labour availability challenges."
Teske continued, "Regardless of the cause of the various headwinds, it is our responsibility to address the issues and restore the company to growth and profitability. As we enter fiscal 2020, we are intensely focused on five key areas to drive improvements in performance:
- First, we are working aggressively to complete the business optimisation program and eliminate the operational inefficiencies to begin realizing the $35 million to $40 million in pre-tax cost savings from the program.
- Second, as we have also announced, we will be consolidating engine production within our plant in Poplar Bluff, Missouri, to streamline operations and adjust production capacity to meet current and anticipated future needs. This initiative will reduce pre-tax expenses by up to $14 million when fully implemented.
- Third, we will be devoting increased time and focus to more fully analysing the dynamics of our market with outside help to position our business for more sustained growth and higher returns. Gaining an outside perspective will help our thinking, planning and actions to further adapt to the continually changing environment so that we are properly positioned as the market continues to change.
- Fourth, we intend to strengthen our balance sheet, with the near-term objectives of improving working capital and lowering debt. With the winding down of investments in our business optimisation initiatives, projected lower capital expenditures and the action announced today to reduce the cash dividend, we will be directing more funds to reduce debt and invest in attractive commercial products and enabling technologies.
- Fifth, we are making solid progress on a debt refinancing which we expect to close before the end of our first fiscal quarter. We believe the refinancing will provide good flexibility as we strengthen the balance sheet and execute our strategy."
Teske concluded, "There is no question that fiscal 2019 was enormously difficult from both a market perspective and our execution on operational excellence. Still, the several foundational changes we implemented advanced our commercial growth and diversification strategy and position us well for the long term. We remain confident in our strategy and view fiscal 2020 as an opportunity to get back on track."
In terms of the 2020 outlook the company says net sales are expected to be within a range of $1.91 billion to $1.97 billion for fiscal 2020, which contemplates midpoint growth of approximately 5.5% over fiscal 2019's performance.
This outlook compares with the company's previous preliminary expectation of approximately $2.01 billion in sales for fiscal 2020.
The revision to the outlook principally relates to the lower base sales for fiscal 2019, a reduction in the company's estimate of the North American market due to near-term disruption caused by channel partner transitions and the prolonged impact of weather on Europe, which has experienced hot and dry conditions in the early months of summer
 |  |
BIG IRISH FENDT FIELD DAYS
To take place in September
A “major display and demonstration of Fendt tractors and machinery” will take place near Dublin in early September.
A “major display and demonstration of Fendt tractors and machinery” will take place near Dublin in early September.
To be staged over two days, the so-called ‘Fendt Field Days’ will run on September 11 and 12 – at Ballyboughal (Eircode: A41 TR25).
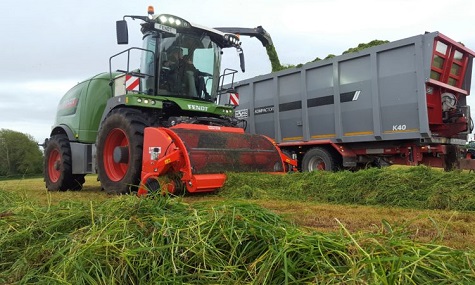
The gates will open at 10:00am and the event will run until 5:00pm each day.
Fendt area sales manager for Ireland and Northern Ireland – Sean Gorman – explained: “We are not just about ‘big tractors that don’t go wrong’; we have worked for many years to establish ourselves at the pinnacle of quality and reliability in the world of farm machinery too.
We feel that Fendt customers – both existing and potential – will appreciate a broader and more in-depth experience of the range than is possible at a traditional trade show. “It’s an opportunity to meet the team and talk to the product specialists.”
The event will also serve as the Irish launch of the latest (MAN-powered) Fendt 900 Vario series tractors; these will apparently feature in the working demonstrations.
According to Sean, there will also be opportunities to test-drive 200, 300 and 500 Vario series tractors – some with front loaders.
At the top end of the spectrum will be an MT series (tracked) machine, plus a 1000 Vario series high-horsepower (wheeled) tractor.
Grass equipment present will include mowers, tedders, rakes, balers, combination baler-wrappers, forage wagons and a self-propelled forager. Sprayers will include trailed and self-propelled versions.
The demonstration site will be split into ‘field stations’, where different activities will be centred. Precautions have apparently been taken to guard against inclement weather; there’ll be a “large marquee”.
Source: Agriland
 |  |
JOHN DEERE ACQUIRES GOLF TECH COMPANY
OnLink software platform
As a result, John Deere will acquire the OnLink platform and service agreements with all existing OnLink customers.
John Deere has announced the acquisition of OnLink, a golf course performance optimisation software platform based in the US.
As a result, John Deere will acquire the OnLink platform and service agreements with all existing OnLink customers.
OnLink is a cloud-based golf course management platform that enables golf courses to collect data and manage equipment, labour, water, chemicals, nutrients and playing conditions.
“We know that data-driven decision making is key to improving agronomic outcomes and financial returns for our golf customers,” says Manny Gan, John Deere’s director of global golf sales and marketing. “This acquisition allows us to continue developing the OnLink platform with the data knowledge we’ve already built, to deliver insightful information to our customers.”
John Deere first began its relationship with OnLink in 2017 when it announced a collaboration with the company. With this acquisition, OnLink will become integrated into John Deere’s suite of technology solutions.
“We are proud and honoured to have an industry leader acquire our software platform,” says Walt Norley, OnLink founder and CEO. “Current and future OnLink users will have the benefit of John Deere, and its strong dealer network, to scale up the platform for further value and efficiency.”
 |  |
ONLINE SERVICES FOR KUHN MACHINES UP TO 20 YEARS OLD
Parts catalogues and operators’ manuals
Essential information for maintenance and repairs, can be obtained by registering a machine’s serial number online, even when dealing with used equipment.
Interactive parts catalogues and operators’ manuals for KUHN machines up to 20 years old can now be accessed through the company’s MyKUHN online customer portal.
Any owner or operator can now obtain essential information for maintenance and repairs, by registering a machine’s serial number on the site, even when purchasing used equipment.
“There’s perhaps a tendency to assume services such as MyKUHN apply only to the new machinery buyer,” says KUHN UK managing director Siân Pritchard, “but the facility is arguably even more valuable to those purchasing a used machine. Having instant access to a user-friendly parts catalogue and up to date operator’s manual should give buyers greater confidence and make any ongoing servicing a lot easier and more cost-effective.”
The MyKUHN online customer portal was first launched in the UK in 2018 and is free to access via any PC, smartphone or tablet where there is access to the internet. In addition to 24/7 technical support, the portal improves KUHN’s post-sales customer service by offering a click and collect genuine spare parts service through local dealers. It also provides a wide range of associated advice and guidance and advanced notice on special offers, product improvements, events and new machine launches.
Once registered to use MyKUHN, customers can tailor the type and level of information they receive by customising their own preferences according to their areas of interest. In this way, users will be able to build their own library of content and will only receive information that is of specific relevance to their machinery fleet or applicable to their farming operations.
 |  |
GIANT FOUR AXLE SILAGE TRAILER
Rolls out of Carlow factory
Well-known manufacturer Smyth Trailers, based in Co. Carlow, has just completed the build of a massive four-axle silage trailer.
Well-known manufacturer Smyth Trailers, based in Co. Carlow, has just completed the build of a massive four-axle silage trailer.
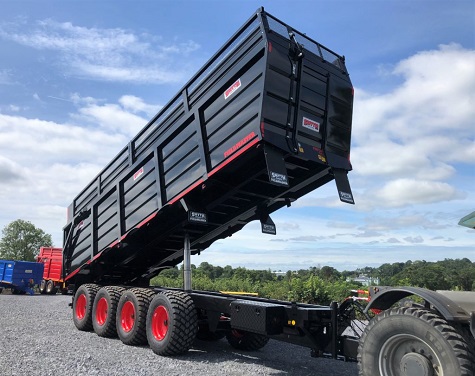
The trailer, which has a rated capacity of 70m³, is destined for Robinson Farms – in New Mexico (US). This customer already runs a fleet of 10 tri-axle Smyth-built trailers.
According to Smyth Trailers, the new four-axle unit is equipped with air/hydraulic brakes, a hydraulic jack, a hydraulic fold-down front creel/panel and a Lincoln automatic greaser.
It’s also fitted with a Distag forced-steering system on the front and rear axles. It’s shod on 600/55-26.5 (‘heavy-duty’) BKT tyres.
Sam Smyth said: “The trailer left here – to start its journey to the US. It’s 32ft long…on the floor. The body is 9ft wide, but the trailer’s overall width is nearly 10ft. It weighs 11tons empty, but can carry about 36tons. It takes 70L of oil to tip it up fully. When it arrives in the US, it’ll be pulled by a new Fendt.”
According to Sam, the price-tag is in the region of €65,000 (plus VAT). Shipping (from Ireland to the US) apparently costs about €8,000.
 |  |
LEMKEN EXTEND AFTER SALES SUPPORT
Offline spare parts catalogue and update stick now available
Lemken have announced they have extended their after sales support for dealers with the release of an offline spare parts catalogue and an update stick.
Lemken have announced they have extended their after sales support for dealers with the release of an offline spare parts catalogue and an update stick.
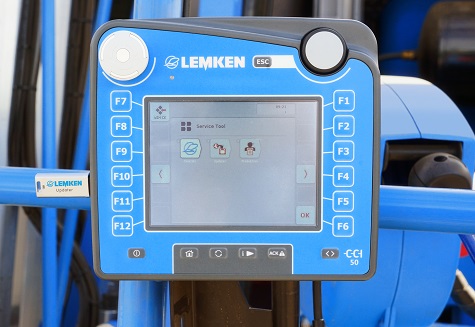
Lemken Update Stick with CCI-50 terminal
The company say that dealers have already enjoyed permanent online access to all product information since last year. The LEONIS information portal additionally provides dealers with exclusive access to spare parts lists, implement data, training documentation and the latest news. This range of services has now been expanded with the release of the offline spare parts catalogue and an update stick.
With LEONIS, LEMKENDOC and the update stick, Lemken says it offers its partners a powerful package of three components to support repairs and ensure that farmers enjoy high implement availability. The Lemken after-sales support package is available worldwide.
The company says the new LEMKENDOC spare parts catalogue provides up-to-date access to original spare parts catalogues at any time. Spare parts can be identified anywhere at any time and then ordered online later. An integrated search for spare parts by serial number and a customisable notes function complement this service, says Lemken, to cut down on the number of enquiries needed and avoid mistakes when ordering.
The company additionally provides its partners with an update stick, which allows service technicians to perform software updates on implements and terminals. The update stick connects regularly to the Lemken software pool and therefore always contains the latest software versions. Technicians also have access to older versions and are able to reset implements to their original settings via a backup and restore function.
 |
|
 |  |
ADVERTISE YOUR JOBS HERE
Amazing success rates!
Advertise your recruitment needs on Serivce Dealer Weekly Update Ireland and reach our targeted audience of recipients every week.
Contact Nikki Harrison for details - 44 01491 837117
|
SHOWCASE YOUR NEW PRODUCTS HERE
Have your new equipment seen first!
Use this Ireland Weekly Update to showcase your new products to our ever-growing community of specialist dealers.
Contact Nikki Harrison - 44 01491 837117
|
|
|